- June 17, 2021
Javier Alzueta: “Our aim is to reduce the carbon footprint as well as improve our customers’ profitability”
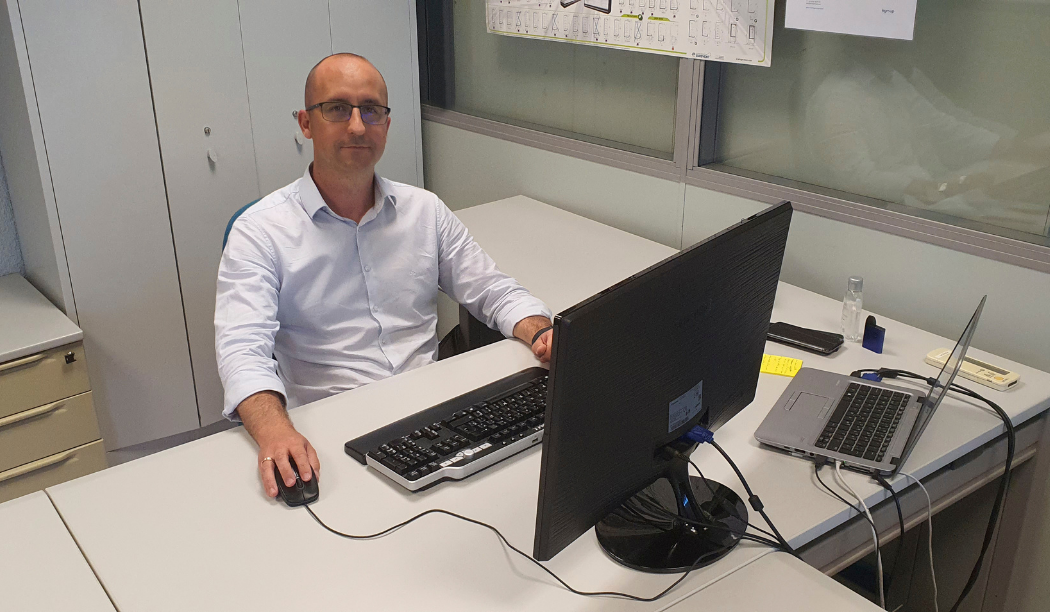
We have talked to Javier Alzueta, our Services & Contracting Manager. He explained all the services he offers and the objectives of this department, which is so important for Koxka.
Tell us about your professional career and your role at Koxka.
– Interestingly enough, my first job was on Koxka’s assembly line 19 years ago. Later I worked in maintenance for automotive companies and once I finished my engineering degree, I worked for 12 years in more than 20 countries in the renewable energy sector, specifically in the services and installations department. Three years ago I returned to my beginnings, to the new Koxka, to join this exciting project as head of Services and Installations.
What does the S&C department currently offer?
– The ultimate goal is that our customers can take care of their business without worrying about the correct functioning of the installation, as well as improving the profitability of their business by reducing energy consumption. To achieve this, we work in two lines: turnkey projects or installations, where we offer the design and implementation of projects adapted to the needs of our customers; and the Service block, where we offer post-warranty services, maintenance, design improvements and spare parts supplies. We do all this thanks to our engineering and installations team that helps us in the design, development and coordination of projects, as well as our branches, our technical department and collaborators who help us in the implementation of these projects.
What value proposition do you offer the market in turnkey projects and installation?
– Our differentiation lies in making the installations more efficient, as well as taking care of the details in the finishes of the installation. By manufacturing the refrigeration units and equipment, as well as having in-house laboratories for testing, we obtain valuable information that helps us to optimise the installations. From the correct dimensioning of an installation to the simple closing of a door can influence the performance of the installation. These are small details, which in the long run have an influence both on how the product looks to our customers and on the electricity bill they will pay, not forgetting the environmental impact that this entails.
And from Service’s point of view?
– For long-term system management, we work with the concept of availability, where our goal is to keep the machines operational for as long as possible. We work on the response time of our technicians, strategic stocks, and processes that help us to minimise the action and maintenance time, but the most important thing that sets us apart is that, once the incident has been resolved, all the departments work together, led by our quality colleagues, to analyse the root cause and define the necessary actions so that it does not happen again. All these actions help to ensure that the Koxka product is a quality product.
You mentioned the environmental impact, what are you doing about it?
– Although I come from the renewable energy sector, I have been very surprised by how committed Koxka is to respecting the environment. Koxka started manufacturing CO2 furniture more than 10 years ago, and nowadays our entire product range works with natural refrigerants such as R290 or CO2. In addition, achieving maximum efficiency with refrigerants that do not damage the ozone layer or contribute to global warming is one of the challenges we are facing. We are already seeing the results in our new CO2 remote product range, where we have probably the most efficient cabinet on the market, which, together with good installation design, means we are reducing our carbon footprint as well as improving our customers’ profitability. And of course, we will continue to learn and improve this efficiency.